Victorinox makes 45,000 Swiss Army Knives per day, almost 10 million per year!
If this incredible fact makes you wonder what goes into the process of manufacturing a Swiss Army Knife, you are not alone.
A Swiss Army Knife is made by an elaborate process that includes making each of the tools as well as the handles separately from respective raw materials and then assembling everything together. The process involves the use of various machines as well as manual effort.
Victorinox has perfected this process during their more than a century-old journey of making Swiss Army Knives. You may also read the history of Victorinox and the Swiss Army knife in this post.
Let’s go through the stages of the development of the Swiss Army Knives in Victorinox’s factory in Ibach, Switzerland.
The Main Raw Material of Swiss Army Knives
Obviously, steel is the main raw material used. Victorinox uses a special blend of stainless steel alloy and doesn’t officially disclose the exact composition.
Big coils of steel that reach the Victorinox factory have to first go through a quality control check before they are put into further processing.
All the various tools in a Swiss Army knife are punched from these steel coils.

Victorinox says that 2500 tonnes of steel are processed every year. They also claim that 95% of the steel used is recycled.
Victorinox imports most of the steel that they use in Swiss Army Knives from 3 countries: France, Germany, and Sweden.
To know more about the properties and the composition of the steel that Victorinox uses, read this article.
Making the Blade
Let us go through the various stages involved in making the most important tool in a Swiss Army Knife: the blade!
Punching out the blade shape
The steel coils are passed through a machine that punches out the 2mm thick blade shapes. It also punches the nail nick or finger groove that is used to pull out the blade from the handles.
16000 blades are punched out from one roll of stainless steel sheet.

The machine can generate 40 tonnes of pressure. Victorinox says that it requires 20 hydraulic presses to produce one blade.
After punching out the blades from the steel sheet, the waste steel is given back to the supplier. This is used for new steel production.
Polishing and Rounding
The punched-out blade shapes are then put into large vibrating containers full of ceramic stones and water. The friction polishes the rough edges of these blade-shaped stainless steel parts.
It takes about five to eight hours to complete the process after which the blades are pulled out of the mix by a large magnet.

Hardening
The hardening process involves heating the blades in large ovens. Victorinox says that a temperature of 1050 degree celsius is used. The heat changes the structure of the steel. This is followed by a quick cool down. The process leads to the formation of a rigid crystalline structure, also known as martensitic steel.
The heat generated in the Victorinox factory is reused to heat the factory as well a 114 other apartments. This is made possible by an innovative heat recovery system in the factory.
Grinding
The grinding process further slims and trims the blades to the final dimension. Utmost care is taken to be as precise as possible otherwise the blades would not fit properly into the slots in the knife. Victorinox says their accuracy is 2 hundredths of a millimeter!

Victorinox uses water from the closed water system in the factory to keep the machines cool during the grinding, polishing, and hardening processes.
The grinding and polishing process produces steel-and-water sludge. The steel is filtered out from the sludge and subjected to very high pressure to form steel cubes. These cubes are given back to the supplier for reuse. Victorinox factories have almost zero steel wastage.
Stamping And Sharpening the Blade
The stamping process imprints the famous Victorinox stamp in the tang of the blades. The Victorinox tang stamp is regarded as a certificate of authenticity of the blade. Over the years since the inception of Victorinox, this stamp has been changed many times.
In fact, the tang stamp is often used to date and identify very old Swiss Army Knives by collectors.
You may read more about Swiss Army Knife identification in this detailed post.
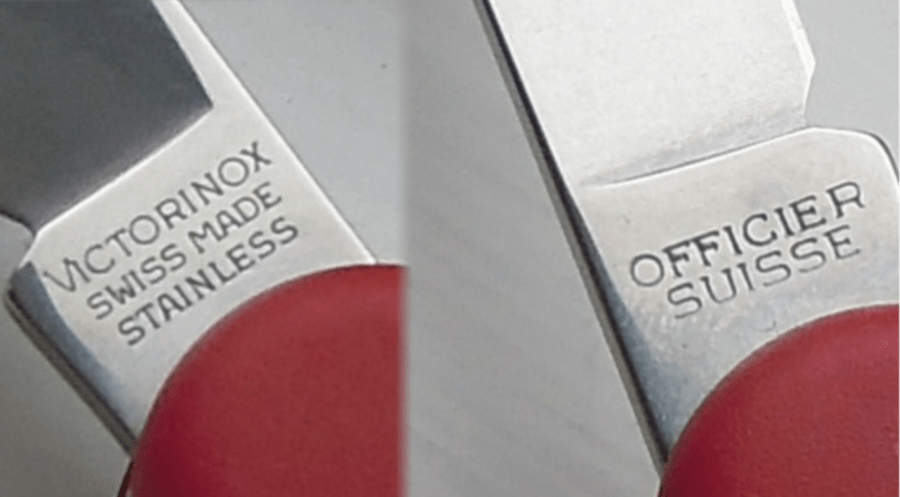
The final sharpening of the blade is done by a process developed by Victorinox in-house. Special grinding wheels are used in the sharpening process. The cutting edge is ground to 15 degrees.
Making the Other Tools
All the other tools are also mass-produced in a similar manner and through more or less similar processes.
Note that the steel hardness of all the tools in a Swiss Army Knife is not the same. Some tools, like the screwdrivers, are made from softer steel compared to the knife.
The composition of Carbon in the steel alloy and the temperature used during the hardening process are slightly altered to get the desired degree of hardness for the different tools.
Assembling the Knife
The blade and the other tools are kept in their respective large boxes once they are ready. In the assembling process, the individual components are methodically put on top of one another, layer by layer, separated by Aluminum separators.
Though Victorinox has automated the assembling process for most of the models, some of the models are still assembled manually by hand.
A skilled and experienced worker in the Victorinox factory can assemble a model like the Swiss Champ in just 3 minutes.
Making the Red Handle Scales
The handle scales are made mainly from synthetic materials like Cellidor plastic and Nylon, though wood and Aluminum are also used.
Cellidor is the most well-known and common material used in many of the models of Swiss Army Knives. The process starts by melting large quantities of very small granules or pellets of the material. The scales are then formed by injection molding.
Red is the most recognizable color of Cellidor scales in Swiss Army Knives. The scales are known to have great longevity and can endure a fair amount of abuse.
To make one scale handle (one side), it takes approximately 8 grams of pellets.
Making the ‘Cross & Shield’ Victorinox Logo
The famous ‘Cross & Shield’ logo is made from a very thin film of metal. Each one of the logo pieces is carefully inspected by microscope to ensure desired quality and thickness.
These are then implanted on the scales by a hot stamping process.

Just like the blade tang stamp, the Victorinox Logo has also changed many times since it was first introduced. The different Victorinox logos from different eras is also used as a factor in the dating and identification of Swiss Army knives.
Attaching The Scales To the Knife
The assembled knife is sandwiched between the two scales and everything is pressed together.
The metal bushings on the outer layer of the knife embed into the grooves on the inner side of the scales which keeps the scales firmly in place.

Once the scales are fitted to the knife, the scale tools like the tweezers and the toothpick are inserted into the scales manually by the workers at the factory.
The assembling process of a typical Swiss Army knife, right from attaching the blade, fitting the screws, and finally adding the scales along with the scales tools involves approximately 35 steps.
Checking And Polishing
This is the last stage of making a Swiss Army Knife and is carried out at the quality control department of the factory. Here, the workers inspect each component of the knife thoroughly.
They open and close the tools individually, and give a final polish by hand with a piece of cloth. To speed up the process, workers use a special pick for opening the tools quickly.
Even minor defects like scratches in the scales can lead to rejection, thus ensuring a very high-quality finished product that actually passes this stage.
After the knives pass the quality control checks, they are packed into their respective boxes along with their respective instruction manuals. Victorinox Swiss Army Knives are exported to 120 countries throughout the world.
You can Assemble your own SAK!
There are two ways by which you can get a feel of assembling a Swiss Army Knife.
There is a SAK Assembly Station at the Victorinox store in Brunnen, Switzerland, which is open to common people. You need to make a prior reservation, however. Here, you can get hands-on experience in assembling a SAK. Experts will guide you through the whole process.
You can also get the SAK engraved here (read this post to know more about engraving a Swiss Army Knife).
The Victorinox Flagship store in Zurich, Switzerland, has a slightly different option. Here they have a make-your-own-knife station.
However, the components are cut out of wood. You can follow a step-by-step guide to assemble the various pieces of wood into a ‘wooden’ Swiss Army Knife. The experience is kind of solving a zigsaw puzzle.
Here is a short video from Victorinox showing the various stages of building a SAK
A hydroelectric power station close to the Victorinox factory supplies all the electricity required to run the various high-powered machines used in the factory to make Swiss Army knives.
Are all Swiss Army Knives made in Switzerland?
All Swiss Army Knives are made in Switzerland in Victorinox factories, with the majority of the knives being made at Ibach and a small number at Delemont.
Victorinox imports the corkscrews from a supplier in France. This is the only tool that isn’t made in-house in the Victorinox factories. (Source: sakwiki.com)
Does Swiss Army Knife have a Lifetime Warranty?
All Victorinox Swiss Army Knives have a lifetime guarantee against any defects in material and workmanship. Victorinox also guarantees all knives and tools to be of first-class stainless steel. Electronic components in Swiss Army Knives have a 2-year guarantee.
The guarantee does not cover the damage caused by misuse, or normal wear and tear. However, you can get the damages (that are not covered by the guarantee) repaired by Victorinox for a service charge.
Are any Swiss Army Knives made in China?
Swiss Army Knives are not made in China. Only Victorinox has been granted the right by the Switzerland Govt. to use the term “Swiss Army” in their products and they do not outsource the assembly or the production of any of the parts of the knife to China.
All products made in China that are sold as Swiss Army Knives are fakes. In fact, every true Swiss Army Knife made to date has been produced in Switzerland, either at Ibach or at Delemont.